Predictive Maintenance Engineer
Information & Technology Management
Date: 19 hours ago
City: Fort Saskatchewan, AB
Contract type: Full time
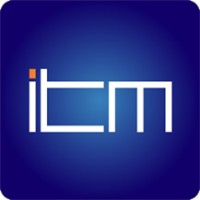
Reference ID R167375 Updated 11/22/2024
Discipline Engineering
Canada
Fort Saskatchewan
N/A
Position Purpose
As a Predictive Maintenance (PdM) Engineer, you will be responsible for the technical accuracy of assessments using PdM-related techniques and the feasibility of recommendations on the mitigation and path forward. You will also provide technical leadership, support, coaching, and mentoring to PdM Craft Team Members and discipline engineers on PdM-related activities.
Accountabilities
If you don’t see yourself fully reflected in every job requirement listed in the posting above, we still encourage you to reach out and apply. Research has shown that women from under-represented groups often only apply when they feel 100% qualified. We are committed to creating a more equitable, inclusive, and diverse company and we strongly encourage applicants of all genders, ages, ethnicities, cultures, abilities, sexual orientations, and life experiences to apply.
Company Description
Shell is a global group of energy and petrochemical companies with about 84,000 employees across more than 70 countries. We aim to meet the world’s growing need for more and cleaner energy solutions in ways that are economically, environmentally and socially responsible. We have expertise in among other exploration, production, refining and marketing of oil and natural gas, and the manufacturing and marketing of oil products, chemicals, electric power, renewables and energy solutions.
As a global energy company operating in a challenging world, we set high standards of performance and ethical behaviors. We are judged by how we act and how we live up to our core values of honesty, integrity and respect for people. Our Business Principles are based on these. They promote trust, openness, teamwork and professionalism, as well as pride in what we do and how we conduct business.
Building on our core values, we aspire to sustain a diverse and inclusive culture where everyone feels respected and valued, from our employees to our customers and partners. A diverse workforce and an inclusive work environment are vital to our success, leading to greater innovation and better energy solutions.
An innovative place to work
There’s never been a more exciting time to work at Shell. Everyone here is helping solve one of the biggest challenges facing the world today: bringing the benefits of energy to everyone on the planet, whilst managing the risks of climate change.
Join us and you’ll add your talent and imagination to a business with the power to shape the future – whether by investing in renewables, exploring new ways to store energy or developing technology that helps the world to use energy more efficiently.
An inclusive place to work
To power progress together, we need to attract and develop the brightest minds and make sure every voice is heard. Here are just some of the ways we’re nurturing an inclusive environment – one where you can express your ideas, extend your skills and reach your potential.
We’re creating a space where people with disabilities can excel through transparent recruitment process, workplace adjustments and ongoing support in their roles. Feel free to let us know about your circumstances when you apply, and we’ll take it from there.
We’re closing the gender gap – whether that’s through action on equal pay or by enabling more women to reach senior roles in engineering and technology.
We’re striving to be a pioneer of an inclusive and diverse workplace, promoting equality for employees regardless of sexual orientation or gender identity.
We consider ourselves a flexible employer and want to support you finding the right balance. We encourage you to discuss this with us in your application.
A rewarding place to work
Combine our creative, collaborative environment and global operations with an impressive range of benefits and joining Shell becomes an inspired career choice.
We’re huge advocates for career development. We’ll encourage you to try new roles and experience new settings. By pushing people to reach their potential, we frequently help them find skills they never knew they had, or make career moves they never thought possible.
Discipline Engineering
Canada
Fort Saskatchewan
N/A
Position Purpose
As a Predictive Maintenance (PdM) Engineer, you will be responsible for the technical accuracy of assessments using PdM-related techniques and the feasibility of recommendations on the mitigation and path forward. You will also provide technical leadership, support, coaching, and mentoring to PdM Craft Team Members and discipline engineers on PdM-related activities.
Accountabilities
- Improve efficiency of the current predictive maintenance/condition-based monitoring program through integration and implementation of the full potential of the existing infrastructure and monitoring systems
- Introduce new technologies to enhance monitoring, diagnosis, and prediction of equipment health
- Interface with the Information, Digital, and Technology team and Americas Chemicals & Products assets on the installation of other wireless instruments and predictive maintenance technology applications
- Assess novel technologies coming to the market for trial and/or use at the site to address known or developing issues
- Responsible for the effectiveness of online vibration monitoring infrastructure, i.e. Bently System 1, Prognost, and software alarm management
- Responsible for effectiveness of Adre 408, Lazer Vibrometer, RDI Motion Amplification and National Instrument Lab View
- Support CTMs (Craft Team Member) in the PdM group with data analysis and field diagnostics, including structural modifications, vibration surveys, source identification, and risk assessment and mitigation
- Second-level condition monitoring support to rotating engineers and (PEI) Pressure Equipment Integrity for complex condition monitoring assessment and troubleshooting
- Interface with Process Automation Controls Optimization /Instrumentation on troubleshooting instrumentation issues, online system issues, monitoring rack issues, e.g. Bently Nevada 3500 racks
- Primary Owner of Bently Nevada System 1 and Prognost VISU.
- Responsible for application issues, configuration, upgrades, and leading MOC (Management of Change) activities for obsolescence
- Support PEI/Fired Equipment disciplines on piping, vessel, boiler, and other asset vibration performance and severity assessment
- Provide input into investment proposals for new predictive maintenance applications
- Support the overall structure and effectiveness of offline vibration monitoring systems, i.e. Analysis Parameter sets, Alarm Limit sets, route management, integration of wireless data, and data transmission rates
- Support turn around activities, motor/pump shop tests, shop balance reports, determining vibration measurement method (brg vs shaft) and making final assessment on machine condition
- Familiarity with online motor current monitoring technologies, setting up shat vibration probes, electric motor vibration analysis and troubleshooting
- Support Projects: instrumentation/monitoring/protection requirements, rotor dynamics/ structural reviews and recommendations, interfacing with vendor/consultants about acceptance criteria, hold points, additional verifications/tests
- System1/Prognost VISU workshops for machinery engineers to maintain and promote advanced features of the software such as statistical software alarm generation, slow roll compensation and orbit overlaid on shaft centerline plot analysis, recip compressor cylinder pressure drift compensation, Peakvue recip comp valve monitoring
- System 1 measurement chain audits: alarm management, data storage management, rack synchronization management
- Prognost audits: system health management, periodic ring buffer reviews
- Responsible for the proper condition, accuracy/calibration, and technical staff training of all instruments and data acquisition systems and software packages owned by PdM
- Develop in-house expertise on PdM-related techniques through 1-1 workshop training, field training, route-based software-driven training, lessons learned sessions, and support to justify external training courses and seminars
- Develop vibration program strategies and PdM-based initiatives
- The vibration program’s focal point
- Influences investment proposals and what the future of the PdM program will look like, including vibration and condition monitoring activities
- Provide support and training on how to effectively use the online software systems
- Troubleshoot online system architecture to find issues along the measurement chain
- Must have legal authorization to work in Canada on a full-time basis for anyone other than your current employer
- You must be a professional engineer with at least 15 years’ experience in mechanical engineering on rotating equipment as well predictive maintenance
- CAT 4 vibration analyst
- Skill-level understanding of online software systems, Emerson, Bently Nevada, Prognost
- Skill/Expert in codes and standards, practices, and technologies in vibration monitoring and safeguarding
- Effective diagnostic and problem-solving skills
- Strong leadership, decision-making, mentorship, coaching, and communication skills
- Can manage evolving priorities and deliver on multiple commitments in a timely manner
If you don’t see yourself fully reflected in every job requirement listed in the posting above, we still encourage you to reach out and apply. Research has shown that women from under-represented groups often only apply when they feel 100% qualified. We are committed to creating a more equitable, inclusive, and diverse company and we strongly encourage applicants of all genders, ages, ethnicities, cultures, abilities, sexual orientations, and life experiences to apply.
Company Description
Shell is a global group of energy and petrochemical companies with about 84,000 employees across more than 70 countries. We aim to meet the world’s growing need for more and cleaner energy solutions in ways that are economically, environmentally and socially responsible. We have expertise in among other exploration, production, refining and marketing of oil and natural gas, and the manufacturing and marketing of oil products, chemicals, electric power, renewables and energy solutions.
As a global energy company operating in a challenging world, we set high standards of performance and ethical behaviors. We are judged by how we act and how we live up to our core values of honesty, integrity and respect for people. Our Business Principles are based on these. They promote trust, openness, teamwork and professionalism, as well as pride in what we do and how we conduct business.
Building on our core values, we aspire to sustain a diverse and inclusive culture where everyone feels respected and valued, from our employees to our customers and partners. A diverse workforce and an inclusive work environment are vital to our success, leading to greater innovation and better energy solutions.
An innovative place to work
There’s never been a more exciting time to work at Shell. Everyone here is helping solve one of the biggest challenges facing the world today: bringing the benefits of energy to everyone on the planet, whilst managing the risks of climate change.
Join us and you’ll add your talent and imagination to a business with the power to shape the future – whether by investing in renewables, exploring new ways to store energy or developing technology that helps the world to use energy more efficiently.
An inclusive place to work
To power progress together, we need to attract and develop the brightest minds and make sure every voice is heard. Here are just some of the ways we’re nurturing an inclusive environment – one where you can express your ideas, extend your skills and reach your potential.
We’re creating a space where people with disabilities can excel through transparent recruitment process, workplace adjustments and ongoing support in their roles. Feel free to let us know about your circumstances when you apply, and we’ll take it from there.
We’re closing the gender gap – whether that’s through action on equal pay or by enabling more women to reach senior roles in engineering and technology.
We’re striving to be a pioneer of an inclusive and diverse workplace, promoting equality for employees regardless of sexual orientation or gender identity.
We consider ourselves a flexible employer and want to support you finding the right balance. We encourage you to discuss this with us in your application.
A rewarding place to work
Combine our creative, collaborative environment and global operations with an impressive range of benefits and joining Shell becomes an inspired career choice.
We’re huge advocates for career development. We’ll encourage you to try new roles and experience new settings. By pushing people to reach their potential, we frequently help them find skills they never knew they had, or make career moves they never thought possible.
How to apply
To apply for this job you need to authorize on our website. If you don't have an account yet, please register.
Post a resumeSimilar jobs
Sales Associate
7-Eleven,
Fort Saskatchewan, AB
2 days ago
Join our growing family of brands! Crew positions are entry level opportunities with both full and part time possibilities to fit your schedule. As one would expect, cash handling, fuel transactions, cleaning, and stocking are part of the role with some foodservice positions specifically tasked with food prep and foodservice safety. What you might not expect is the camaraderie of...
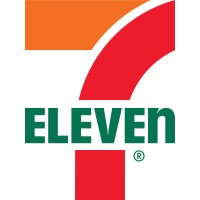
Safety Specialist
Information & Technology Management,
Fort Saskatchewan, AB
1 week ago
Reference ID R166714 Updated 11/11/2024Health, Safety, Security, and EnvironmentCanadaFort SaskatchewanN/APosition PurposeAs a Safety Specialist, you will be responsible for providing interpretation of, and support to, the business in implementing the operational safety standards. Coach and mentor front line leaders and the frontline on owning/delivering HSE performance.AccountabilitiesProvide safety training, auditing, plant safety inspections, and safety support to the Production, Maintenance, Projects...
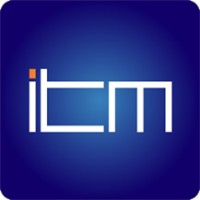
Unit Inspector - NDE
Information & Technology Management,
Fort Saskatchewan, AB
1 week ago
Reference ID R166842 Updated 11/13/2024Discipline EngineeringCanadaFort SaskatchewanN/APosition PurposeAbout The OpportunityShell Canada is seeking a Unit Inspector Non-Destructive Examination (NDE) to join their Shell Scotford Mechanical Engineering team.This team member maintains the integrity of pressure equipment at Scotford manufacturing facilities. The role manages aspects of NDE, inspection, materials, welding, quality control, quality assurance, equipment design, procedure review, and creating/updating pressure equipment...
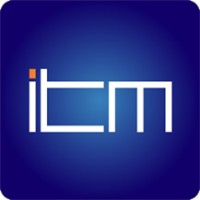