Plant Manager
Highbridge Human Capital
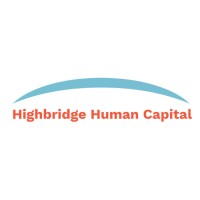
THE COMPANY
Founded in 2017, We Are One Composites is a proudly Canadian company leading the way in advanced composite manufacturing for the mountain bike industry. Located in Kamloops, BC, we design, engineer, prototype, test, and manufacture world-class mountain bike products—all under one roof. Known for our innovation, meticulous craftsmanship, and unwavering commitment to quality, We Are One is redefining performance standards in the cycling world while expanding our in-house manufacturing capabilities.
THE OPPORTUNITY
We Are One Composites is currently seeking an exceptional Plant Manager to lead our manufacturing operations in Kamloops, BC. This is an exciting opportunity for a seasoned operations leader to drive production excellence, optimize processes, and foster a culture of safety, quality, and collaboration. Reporting to the Operations Director, the Plant Manager will oversee all facets of the production process. They will be responsible for ensuring operational efficiency, meeting performance targets, and advancing innovation within a fast-moving, values-driven organization.
The ideal candidate will bring a proven track record in operational leadership, technical expertise in manufacturing, strong troubleshooting skills, and a strategic mindset that aims to improve production goals while pursuing broader business objectives.
POSITION DESCRIPTION
Reporting to the Operations Director, the Plant Manager is responsible for the day-to-day leadership of all manufacturing-related staff at our manufacturing facility. This includes leading the production team, managing staffing demands, driving KPIs, ensuring safety and quality compliance, and spearheading continuous improvement initiatives. The Plant Manager will be critical in creating a cohesive environment and encouraging all manufacturing staff to achieve production targets and deliver exceptional products to our customers.
KEY RESPONSIBILITIES
Leadership & Employee Management
- Manage and support all employees on the factory floor, ensuring they have the resources and training needed to succeed.
- Lead by example, fostering a positive and productive work environment.
- Build strong relationships with team members to promote trust, open communication, and alignment with company goals.
- Address employee concerns promptly and effectively, creating a culture of inclusivity and respect.
- Identify skill gaps and organize training opportunities to develop a highly skilled and versatile workforce.
- Mentor team members to take ownership of their roles and contribute to overall success.
Production Oversight & Optimization
- Collaborate with leadership to set clear, achievable production targets and KPIs.
- Monitor daily operations to ensure all teams are on track to meet these objectives.
- Identify and implement opportunities for improving workflows, reducing downtime, and increasing output.
- Partner with teams to troubleshoot issues and find practical, efficient solutions.
- Act as a resource for each production team, assisting with challenges and ensuring smooth operations.
- Regularly evaluate team performance, celebrating successes and addressing areas needing improvement.
Fostering Innovation & Recognition
- Promote a mindset of innovation and problem-solving across the factory floor.
- Encourage employees to share ideas for enhancing efficiency, quality, and safety.
- Recognize and reward employee contributions to foster morale and engagement.
- Create and implement programs that celebrate milestones and achievements.
CORE COMPETENCIES FOR SUCCESS
Leadership & Communication
- Demonstrates the ability to lead by example, setting high personal and professional standards.
- Fosters a shared sense of purpose and direction, motivating employees to achieve their best.Skilled at addressing and resolving conflicts constructively to maintain team harmony.
- Strong verbal and written communication skills, ensuring clear and concise instructions.
Operational Expertise & Problem-Solving
- Efficiently allocates personnel, equipment, and materials to meet production demands.
- Develops and manages comprehensive production schedules to optimize workflows.
- Applies analytical thinking to identify root causes of production challenges.
- Utilizes production metrics and data to guide decisions and track improvements.
Continuous Improvement & Innovation
- Experienced in identifying waste and inefficiencies, implementing lean tools like 5S, Kaizen, or Six Sigma.
- Regularly reviews workflows to identify areas for optimization and increased output.
- Encourages employees to share ideas and participate in improvement initiatives.
Employee Engagement & Development
- Creates a cohesive, collaborative environment where employees feel valued and motivated.
- Develops tailored training programs to up-skill employees and prepare them for career growth.
- Implements recognition programs to celebrate milestones and individual achievements.
Technical Acumen & Compliance
- Comprehensive understanding of production equipment, workflows, and processes.
- Champions a safety-first culture, ensuring compliance with all health and safety regulations.
- Develops, tracks, and analyzes key performance indicators (KPIs) to measure operational success.
QUALIFICATIONS
EDUCATION
- Bachelor’s degree in Engineering, Manufacturing Management, or a related technical field.
- Certifications in Lean Manufacturing, Six Sigma, or equivalent are highly valued.
EXPERIENCE
- Minimum of 10 years of experience in a manufacturing environment, including 7+ years in a leadership role such as Plant Manager or General Manager.
- Strong leadership skills with a history of building and mentoring high-performance teams.
- Proven experience managing budgets, KPIs, and operational strategies for continuous improvement.
- You anticipate and plan for changes to current organizational policies, practices, systems, etc. needed to move in new strategic directions and to ensure long-term success.
- You demonstrate a high level of integrity, strong interpersonal skills, the ability to build consensus, and a strong emphasis on responsibility and accountability.
- You have strong decision-making skills and the determination to see projects through to the end. Able to deliver near-term wins while building towards a larger strategic vision.
- Self-sufficiency, reliability, and ability to lead through building trust and inspiring people to be bold.
- Strong communication skills with the ability to collaborate with both internal and external stakeholders.
TOOLS AND SYSTEMS
- ERP systems for production planning, scheduling, and resource management.
- CAD/CAM tools and CNC machinery.
- Lean Manufacturing and Six Sigma methodologies.
METRICS FOR SUCCESS
- Achievement of production quotas and operational KPIs.
- Continuous improvement in efficiency, downtime reduction, and cost management.
- Maintenance of rigorous safety and quality standards.
- Improved team engagement, retention, and professional development outcomes.
TOTAL REWARDS
- Salary range of $95,000 - $110,000, based on skill set and experience.
- Comprehensive health and wellness benefits.
- Opportunities for leadership development and professional growth.
- An innovative, collaborative, and values-driven work environment.
How to apply
To apply for this job you need to authorize on our website. If you don't have an account yet, please register.
Post a resumeSimilar jobs
Customer Consultant
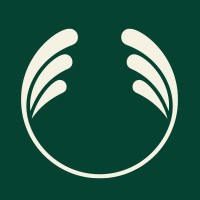
Dishwasher
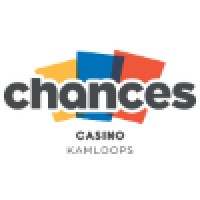
Health Care Aide
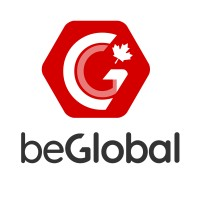