Director, Supply Chain - Supply Planning
The Coca-Cola Company
Date: 3 weeks ago
City: Peterborough, ON
Contract type: Full time
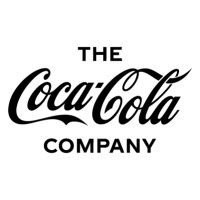
As The Coca-Cola Company’s ambition to provide Beverages for Life and our North America’s portfolio continues to become more complex to keep up with changing consumer taste, our supply chain and operations must be able to keep up with building new capabilities and evolve, while sustaining our base business. The Company’s focus on both the top-line growth (Net Revenue) and bottom-line growth (Operating Income) emphasizes the importance of planning, optimizing our supply chain, and constantly evolving to become as effective and efficient as possible.
The National Supply, Inventory and Orbit Planning for our Nutritional lines of products (e.g., fairlife, Minute Maid, Simply, Fuze Tea and more) continues to become more critical in our midterm planning and day-to-day operations in order to balance demand and supply, capacity constraints and inventory builds, especially as we execute the Asset Light strategy in the North America Operating Unit (NAOU), forcing greater collaboration and orchestration within the OU, as well as with co-man partners.
With growing complexities in our portfolio and operations, the Director of National Supply, Inventory, and Orbit Planning team must lead various processes. Those processes include strategic events like the National Supply Review, the Canadian S&OP routines with Sales and Category leadership, as well as Executive S&OP. The Director must be flexible to also lean in to guide and develop a team of Supply Planning Leaders and Managers on tactical matters. The Director will help develop, track, measure and improve performance against aligned KPIs.
The Director must inspire and lead deliberately, strategically, and methodically with a razor-sharp focus: continuously improve our plans to drive operating effectiveness and overall supply chain performance through scenario planning, internal and cross functional collaboration, developing next-generation team members and technologies. As more automation becomes the expectation, the Director must determine the best way to balance technology with human resources.
Function Related Activities/Key Responsibilities
Midterm Capacity & Supply Planning
Leadership; Supply Chain; Innovation; Supply Chain Planning (SCP); Manufacturing; Communication; People Management; Project Management; Planning; Performance Standards; Logistics; Process Improvements; Teamwork; Collaboration
Pay Range:$143,000 - $166,000
Base pay offered may vary depending on geography, job-related knowledge, skills, and experience. A full range of medical, financial, and/or other benefits, dependent on the position, is offered.
Annual Incentive Reference Value Percentage:30
Annual Incentive reference value is a market-based competitive value for your role. It falls in the middle of the range for your role, indicating performance at target.
The National Supply, Inventory and Orbit Planning for our Nutritional lines of products (e.g., fairlife, Minute Maid, Simply, Fuze Tea and more) continues to become more critical in our midterm planning and day-to-day operations in order to balance demand and supply, capacity constraints and inventory builds, especially as we execute the Asset Light strategy in the North America Operating Unit (NAOU), forcing greater collaboration and orchestration within the OU, as well as with co-man partners.
With growing complexities in our portfolio and operations, the Director of National Supply, Inventory, and Orbit Planning team must lead various processes. Those processes include strategic events like the National Supply Review, the Canadian S&OP routines with Sales and Category leadership, as well as Executive S&OP. The Director must be flexible to also lean in to guide and develop a team of Supply Planning Leaders and Managers on tactical matters. The Director will help develop, track, measure and improve performance against aligned KPIs.
The Director must inspire and lead deliberately, strategically, and methodically with a razor-sharp focus: continuously improve our plans to drive operating effectiveness and overall supply chain performance through scenario planning, internal and cross functional collaboration, developing next-generation team members and technologies. As more automation becomes the expectation, the Director must determine the best way to balance technology with human resources.
Function Related Activities/Key Responsibilities
Midterm Capacity & Supply Planning
- Provide a North American vision of the needs and requirements to the regional supply networks. This role will be the face of supply planning for the Canadian region as well as the lead voice for our chilled non-Simply PET products in the US.
- Assemble, design, and activate the lowest cost supply network solution, while preparing additional contingent scenarios.
- Works closely with Supply Chain Optimization & Infrastructure Planning Team and Director Integrated Logistics Planning on E2E asset and sourcing projects
- Build, maintain, and communicate national capacity models by plant/line for each assigned brand/package.
- Consider scenarios when emergencies emerge due to unforeseen events (e.g., weather, breakdowns, material shortages, etc.) to find the best-next options to supply customer demand/orders while minimizing costs.
- Play the SME role for assigned new product introductions, product changes, and product discontinuations, including participating in project meetings, submitting item set-up requests, tracking materials planning, publishing factsheets and assembling product write-off estimates.
- Establish planning strategy for assigned product lines and supply network structure and work with Regional Planning to populate and maintain parameter settings in system tools to support the strategy and maximize the planning groups efficiency & accuracy.
- Present business case to execute on seasonal/peak inventory pre-builds.
- Lead efforts on implementing optimal multi-echelon inventory recommendations from Llamasoft/Lyric with collaboration with Region and Copackers to free up cash from working capital.
- Minimize costs and maximize customer service levels.
- Track and manage performance against the target inventory levels to improve NAOU's overall cash position.
- Coach and collaborate with Regional Planners to best manage product supply across the Regional or National network.
- Understand key supply chain performance levers (e.g., on-time delivery, total supply chain cost, operational feasibility, etc.) and seek solutions to improve these metrics.
- Report out performance results, current business status, and future risks via Weekly Hot Spots, S&OE and S&OP meetings.
- Provide structured and creative analyses to identify performance improvement opportunities.
- Collaborate extensively with Network/Sourcing and Inventory Optimization Leader to operationalize recommendations from modeling software (Llamasoft/Lyric) and track actual execution and results vs. potential opportunities.
- Collaborate with Forecast COE, Demand Planning, and Region teams to identify upcoming risks proactively to determine contingencies.
- Mitigate risks to maximize product availability while minimizing supply chain costs with specific and actionable recommendations.
- Orchestrate and execute contingency plans with collaboration and support from regional teams and Category Commercialization.
- Leverage these routines to clearly communicate risks, opportunities, and contingency plans.
- Exercise PDCA (Plan-Do-Check-Adjust) to identify root causes and improvement opportunities.
- Bachelor's Degree in Business, Supply Chain, Finance, or Operations
- Masters Preferred
- 15+ Years in Supply Chain Management, Planning, Commercialization or Operations
- 5+ Years in People Management
- Project Management
- Business Management Technology Implementation
- Anaplan, SAP, ORI, Integrated Business Planning (IBP), Lyric experience preferred Functional Skills
- Analytical: data processing into insights and decision-making recommendations.
- Communication: oral, written, presentation
- PDCA (Plan, Do, Check, Adjust): Closing the loop on all supply planning activities.
Leadership; Supply Chain; Innovation; Supply Chain Planning (SCP); Manufacturing; Communication; People Management; Project Management; Planning; Performance Standards; Logistics; Process Improvements; Teamwork; Collaboration
Pay Range:$143,000 - $166,000
Base pay offered may vary depending on geography, job-related knowledge, skills, and experience. A full range of medical, financial, and/or other benefits, dependent on the position, is offered.
Annual Incentive Reference Value Percentage:30
Annual Incentive reference value is a market-based competitive value for your role. It falls in the middle of the range for your role, indicating performance at target.
How to apply
To apply for this job you need to authorize on our website. If you don't have an account yet, please register.
Post a resume