Intermediate Technician– Abbott Point of Care (Ottawa)
Abbott Laboratories
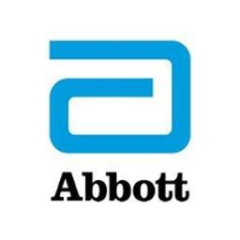
About Abbott
Abbott is a global healthcare leader, creating breakthrough science to improve people’s health. We’re always looking towards the future, anticipating changes in medical science and technology.
Working at Abbott
At Abbott, you can do work that matters, grow, and learn, care for yourself and family, be your true self and live a full life. You will have access to:
Career development with an international company where you can grow the career you dream of.
A company recognized as a great place to work in dozens of countries around the world and named one of the most admired companies in the world by Fortune.
A company that is recognized as one of the best big companies to work for as well as a best place to work for diversity, working mothers, female executives, and scientists.
We offer flexible work policies that allows a healthy balance between personal and professional life
We invest in the development of our employees through training and growth opportunities
We foster an environment where every voice is heard and valued
The Opportunity
This position works out of our Ottawa, Ontario location in the Point of Care, Diagnostics division. We’re empowering smarter medical and economic decision making to help transform the way people manage their health at all stages of life. Every day, more than 10 million tests are run on Abbott’s diagnostics instruments, providing lab results for millions of people.
As an Intermediate Technician in Cartridge Assembly, you’ll have the chance to be a key contributor in ensuring manufacturing output, quality, and compliance of i-STAT cartridges. In this role you will be responsible for achieving all key performance indicators (KPI) for the Assembly Line, including Safety, Quality, Equipment Reliability, Line Output, Line Yield, Material Use Variance, OEE, and Productivity. As an Intermediate Technician in Cartridge Assembly, you’ll have the chance to be a key contributor in ensuring manufacturing output, quality, and compliance of i-STAT cartridges. In this role you will be responsible for achieving all key performance indicators (KPI) for the Assembly Line, including: Safety, Quality, Equipment Reliability, Line Output, Line Yield, Material Use Variance, OEE, and Productivity.
What You’ll Do
Monitor and action Line KPI’s such as Cartridges per Hour (CPH), Overall Equipment Effectiveness (OEE), Line Yield, Output, Faults, and Downtime through collaboration with Operational, Technician, and Engineering stakeholders to resolve issues and ensure that daily / weekly / monthly performance targets are being achieved.
Execute Preventative Maintenance as per documented procedures.
Provide technical training to Autonomous Maintenance Techs within the Operations team.
Maintain a technical and operational level of training to sustain and operate manufacturing lines as needed.
Carry a 2-way radio and actively respond to front-line calls for equipment support.
Provide technical support for Control Systems and Automated Equipment. This will include PLC’s, PC’s, Inspection Systems and motion control systems.
Set-up, troubleshoot and implement improvements on End-of-Arm Tooling and staging nests.
Diagnose issues on precision mechanical systems consisting of high tolerance tooling driven by pneumatic and servo motor driven systems; performing appropriate adjustments or repairs to ensure smooth operation.
Implement repairs derived from a work order system. Evaluate work order details to provide man / hour estimates to equipment technician team leader to support planned maintenance activity.
Follow diagnostic aids to establish the root cause of equipment faults.
Utilize Equipment downtime data to identify and implement the corrections needed to sustain optimum equipment performance.
Sufficient knowledge to understand the safety risks associated with high-speed automated equipment and is able to support the implementation of corrective actions as defined by the EHS Committee.
Work safely within the Ontario Occupational Health & Safety Act & Regulations.
Performs complex work, involving interpretation of information, techniques and methodologies for successful completion.
Generally works independently in accordance with standard practices, policies and precedents. Supervisory direction is available when necessary.
Plans and organizes work/project assignments of a substantial variety and complexity. Initiates or maintains a schedule for projects and project milestones. Establishes priorities for individual and project assignments.
Solve complex problems requiring extensive interpretation of procedures and practices. Selects methods and practices to solve problems using ingenuity, creativity and a high degree of independent action and initiative. May develop and implement projects from concept to completion.
Communicates ideas and suggestions for improving processes to leadership and actively participates in implementing solutions. Updates associated documentation, as necessary.
Understands and complies with Quality and EH&S policies, procedures and guidelines.
Safeguards the environment and facilitates a safe and healthy workplace culture.
Work with Line Machine Operators to develop best practices for Line Operation to achieve KPI targets and standardize performance across the shifts.
Support Line Operation and Maintenance through certification to develop subject matter expertise, guide improvement prioritization, and ensure achievement of production targets.
Utilize Structured Problem Solving to drive to root cause on ongoing Performance and Quality issues and identify, develop, and implement robust and pragmatic solutions to avoid recurrence.
Ensure the compliant state of Line through development/sustaining of systems for Good Record Keeping practices for all manufacturing data and sustaining of Validations, verifications, calibrations, and design changes associated with the Line.
Shift - Night Shift C, Sunday, Monday, Tuesday and every other Saturday from 6:30 PM to 6:30 AM.
Required Qualifications
College Diploma (two-year program) in an Electrical, Electronic, Mechanical, Robotic or similar discipline.
Minimum of one plus years of relevant work experience in a fast paced and regulated manufacturing environment.
Proven technical, creative, and implementation skills to contribute to continuous improvement of equipment / process design, quality, cost, and reliability.
Ability to balance day-to-day production needs with completing longer term projects.
Strong interpersonal, organizational, written, and verbal communication skills are mandatory.
Analytical skills, creativity and innovative approach to problem solving.
Ability to determine required analysis to make practical, objective decisions about the best solutions to problems.
Effective at planning and coordinating, with excellent time-management skills.
Ability to build and use an effective network of people inside and/or outside the organization to give and receive information and to accomplish work objectives.
Strong interpersonal, communication and presentation skills; able to deal effectively with people on all organizational levels and work in a team environment across departments.
Enthusiasm and propensity to continuous learning and experimentation.
Preferred Qualifications
Experience with automated assembly processes, machine vision, seal and adhesion technology, product packaging, injection molded components, or laser cutting.
Experience with ISO/FDA regulations, Current Good Manufacturing Practice 21 CFR Part 820, user requirements specification, process qualification, risk management/PFMEA methods, Quality / CAPA systems.
Familiarity with experimental design, data analysis, process control, statistical analysis, root cause analysis (6M’s/ 5 Why’s), six sigma.
Experience with software packages such as Solidworks, SQL Server Management, PowerBI, and PLC/HMI Programming packages for Allen Bradley, Omron, Yaskawa or Siemens platforms.
Follow your career aspirations to Abbott for diverse opportunities with a company that can help you build your future and live your best life. Abbott is an Equal Opportunity Employer, committed to employee diversity. Connect with us at www.abbott.com, on Facebook at www.facebook.com/Abbott and on Twitter @AbbottNews and @AbbottGlobal.
How to apply
To apply for this job you need to authorize on our website. If you don't have an account yet, please register.
Post a resume